Clean rooms are required to maintain positive pressure so particulates like dust, dirt and debris are kept away from highly sensitive products while being manufactured. Clean rooms are required in a number of industries; from pharmaceutical manufacturing to industrial and food preparation.
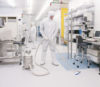
The TV2 Clean Room Monitor is a highly accurate and cost effective way to monitor clean room pressure. The TV2 Clean Room Monitor can measure pressure between ±0.5″ of water with an accuracy of +/- 0.002” of water. Other features include a 16-bit analog to digital converter, ability to chart and record temperature and relative humidity. The monitor can be calibrated by the manufacturer, or alternatively, higher accuracy can be achieved through user calibration.
About ISO Cleanroom Standards
Currently, there are global cleanroom classifications and standards set forth by the International Standards Organization (ISO). Before these current regulations, the U.S. General Service Administration’s standards (known as FS209E) were applied across the board – worldwide. Over time, the need for international standards grew, so the ISO established a technical committee and several working groups to establish it’s own set of standards for the cleanroom industry as a collective.
FS209E contains six classes, while the ISO 14644-1 classification system adds two cleaner standards and one dirtier standard (see chart below). The “cleanest” cleanroom in FS209E is referred to as Class 1; the “dirtiest” cleanroom is a class 100,000. ISO cleanroom classifications are rated according to how much particulate of specific sizes exist per cubic meter (see second chart). The “cleanest” cleanroom is a class 1 and the “dirtiest” a class 9. ISO class 3 is approximately equal to FS209E class 1, while ISO class 8 approximately equals FS209E class 100,000.
In November 2001, Federal Standard 209E was superseded by the new ISO 14644-1 international standards. References to FS209E are still used; the comparison chart below illustrates the relationship between the two standards.
Particulate Cleanliness Class Comparison:
ISO 14644-1 |
FEDERAL STANDARD 209E |
ISO Class |
English |
Metric |
ISO 1 |
|
|
ISO 2 |
|
|
ISO 3 |
1 |
M1.5 |
ISO 4 |
10 |
M2.5 |
ISO 5 |
100 |
M3.5 |
ISO 6 |
1,000 |
M4.5 |
ISO 7 |
10,000 |
M5.5 |
ISO 8 |
100,000 |
M6.5 |
ISO 9 |
|
|
Particulate Cleanliness Classes (by cubic meter):
CLASS |
Number of Particles per Cubic Meter by Micrometer Size |
|
0.1 micron |
0.2 micron |
0.3 micron |
0.5 micron |
1 micron |
5 microns |
ISO1 |
10 |
2 |
|
|
|
|
ISO2 |
100 |
24 |
10 |
4 |
|
|
ISO3 |
1,000 |
237 |
102 |
35 |
8 |
|
ISO4 |
10,000 |
2,370 |
1,020 |
352 |
83 |
|
ISO5 |
100,000 |
23,700 |
10,200 |
3,520 |
832 |
29 |
ISO6 |
1,000,000 |
237,000 |
102,000 |
35,200 |
8,320 |
293 |
ISO7 |
|
|
|
352,000 |
83,200 |
2,930 |
ISO8 |
|
|
|
3,520,000 |
832,000 |
29,300 |
ISO9 |
|
|
|
35,200,000 |
8,320,000 |
293,000 |
In cleanrooms, particulate concentration will change over time — from the construction and installation of equipment to its operational status. ISO delineates three cleanroom classification standards: as-built, at-rest and operational. As people are added to the equation, particulate levels rise even further in the “operational” cleanroom.
ISO 14644-2 describes the type and frequency of testing required to conform to certain standards. The following tables indicate mandatory and optional tests.
Required Testing (ISO 14644-2)
Schedule of Tests to Demonstrate Continuing Compliance |
Test Parameter |
Class |
Maximum Time Interval |
Test Procedure |
Particle Count Test |
<= ISO 5 |
6 Months |
ISO 14644-1 Annex A |
> ISO 5 |
12 Months |
Air Pressure Difference |
All Classes |
12 Months |
ISO 14644-1 Annex B5 |
Airflow |
All Classes |
12 Months |
ISO 14644-1 Annex B4 |
Optional Testing (ISO 14644-2)
Schedule of Additional Optional Tests |
Test Parameter |
Class |
Maximum Time Interval |
Test Procedure |
Installed Filter Leakage |
All Classes |
24 Months |
ISO 14644-1 Annex B6 |
Containment Leakage |
All Classes |
24 Months |
ISO 14644-1 Annex B4 |
Recovery |
All Classes |
24 Months |
ISO 14644-1 Annex B13 |
Airflow Visualization |
All Classes |
24 Months |
ISO 14644-1 Annex B7 |
In addition to ISO 14644-1 and ISO 14644-2, eight other cleanroom standards documents exist, as well as three specific to biocomtamination applications.
ISO Document |
Title |
ISO 14644-1 |
Classification of Air Cleanliness |
ISO 14644-2 |
Cleanroom Testing for Compliance |
ISO 14644-3 |
Methods for Evaluating and Measuring Cleanrooms and Associated Controlled Environments |
ISO 14644-4 |
Cleanroom Design and Construction |
ISO 14644-5 |
Cleanroom Operations |
ISO 14644-6 |
Terms, Definitions and Units |
ISO 14644-7 |
Enhanced Clean Devices |
ISO 14644-8 |
Molecular Contamination |
ISO 14644-9 |
Surface Cleanliness by Particle Concentration |
ISO 14644-10 |
Surface Cleanliness by Chemical Concentration |
ISO 14698-1 |
Biocontamination: Control General Principles |
ISO 14698-2 |
Biocontamination: Evaluation and Interpretation of Data |
ISO 14698-3 |
Biocontamination: Methodology for Measuring Efficiency of Cleaning Inert Surfaces |
USP Cleanrooms
USP regulated cleanrooms are designed with positive pressure sensors and monitoring systems to meet (or attempt to meet) strict USP standards.
Under USP 797 regulations, compounding pharmacies are required to compound sterile preparations (CSPs) utilizing a laminar flow workstation within a clean room. It is also important for the exterior environment of the Laminar flow workstation to be free from particulates using a TV2 Cleanroom Monitor.
Sterile compounding is classified into 3 risk groups: Low Risk, Medium Risk, and High Risk. If a company prepares CSPs, which meet the definition of the specific categories, described in USP Chapter 797 you must comply with USP 797. The standards are intended to apply to all persons who prepare CSPs and all places where CSPs are prepared including physicians offices.
The USP 797 cleanroom requirements are general in nature, but refer to the International Standards Organization ISO-14644 standards for cleanrooms. To achieve USP 797 compliance, pharmacies must perform sterile drug compounding within an ISO 5 (Class 100) hood environment, enclosed within a larger compounding “Buffer Zone” of ISO 7 (Class 10,000) positive pressure controlled-air environment (Cleanroom).
For example: an ISO 5 compounding environment can be maintained utilizing a Laminar Flow Workstation within an existing ISO 7 cleanroom, or by designing and building a new ISO 5 cleanroom. Maintaining the proper positive pressure within the cleanroom must be evaluated and taken into consideration when designing a sterile cleanroom operating environment. The TV2 Cleanroom Monitoring System helps cleanroom manufacturers and designers comply with strict ISO and USP standards of operation.
Summary
In most large-scale FDA-regulated pharmaceutical manufacturing operations, it is required that the product be manufactured in a clean room classified between Class 100 and Class 100,000. In an operation where medical tubing is being extruded, the classification would likely be Class 100,000. In a process where inject-able drugs are being manufactured, the classification would most likely be Class 100 or Class 1000.
The purpose of the clean room is to eliminate contamination by particulate counts, some of which could potentially contain microorganisms or bio-toxins. Cleanrooms provide a controlled physical environment with a close monitoring of temperature, pressure and humidity. Unlike most existing products on the market, the TV2 Cleanroom Monitor can measure, chart and digitally record all three variables simultaneously.
For cleanroom manufacturers and operators – monitoring these these three variables is no easy task. The intake air must be filtered and moisture and/or heat added or removed depending on the manufacturing taking place. In most cases, large fans located above the clean room force air through an elaborate filtering system. Likewise, air must be used to remove any contamination introduced by the occupants and materials taken into the clean room.
Of the three parameters being measured (temperature, positive pressure and relative humidity RH), pressure is the most critical to the proper functioning of the ISO/USP compliant clean room.
Since most clean room pressure sensors and monitoring systems operate at very low pressure differentials, normally in the range of 0.1 to 0.25 inH 2O, it is imperative that cleanroom manufacturers incorporate a solution that will consistently provide accuracy. The TV2 Cleanroom Monitor measures pressure between +1 inH 2O and -1 inH 2O with an accuracy of +/- 0.025 inH 2O.
The TV2 Cleanroom Monitoring System includes a high-accuracy propietary positive and negative pressure sensor, a temperature sensor (available in multiple spec ranges) and a relative humidity/RH sensor. Measurements are taken at chosen intervals, and all data is recorded with battery backup. Featured on-screen color coding immediately notifies clean room operators and employees of any “unsafe” conditions before entry and possible cleanroom contamination.